Many different types of manual valves are used in industrial applications worldwide. The following article will cover the general mechanism and function of the most typical of these valves used in steam systems, such as ball valves, butterfly valves, globe valves, gate valves, and diaphragm valves.
Manufactured Steam Products We’re proud to work with Watson McDaniel, an ISO 9001 Quality Certified manufacturer, whose globally recognized and time-tested products offer maximum efficiency. From sophisticated control valves to standard steam traps, we have the steam specialty products you need at a cost you can afford. The air vent on a steam radiator allows air in the cooled radiator to be pushed out to make room for the incoming steam as the heating cycle begins. The hissing sound of the air venting from the valve is a sign of normal operation, but the noise should stop once the radiator comes up to temperature and the vent closes, thereby retaining steam in the radiator so it can give up its heat.
Hoffman Steam Air Vent 40, 1/8' Angle Steam Radiator Air Valve 401440. 4.5 out of 5 stars 113. Get it as soon as Mon, Apr 5. FREE Shipping by Amazon. Productivity, efficiency and accurate control are the objective of any steam system. The secret to this is to match the characteristics of the valve to the application. When this match is made you accomplish reliable and accurate control. Manufactured Steam Products. We’re proud to work with Watson McDaniel, an ISO 9001 Quality Certified manufacturer, whose globally recognized and time-tested products offer maximum efficiency. From sophisticated control valves to standard steam traps, we have the steam specialty products you need at a cost you can afford. MADE IN THE USA.
According to JIS, a valve is defined as:
A generic name for a device with a moveable feature* that opens and closes a passageway in order to allow, prevent or control the flow of fluids.
*The moveable feature referred to is the 'valving element'.
Manual Valves by Construction Type
The valving element rotates in the passageway to stop flow.
Steam Valve Index Return Policy
For further details jump down to: ball valve, butterfly valve
The valving element acts as a 'seal' or 'plug' in the passageway to stop flow.
For further details jump down to: globe valve
The valving element is 'inserted' into the passageway to stop flow.
Steam Rated Ball Valve
For further details jump down to: gate valve
The valving element is 'pinched' against the passageway from the outside to stop flow.
For further details jump down to: diaphragm valve
Ball Valves
Ball valves offer very good shut-off capabilities. A simple quarter-turn (90°) completely opens or closes the valve. This characteristic minimizes valve operation time and decreases the likelihood of leakage due to wear from the gland seal.
Ball valves can be divided into two categories: reduced bore and full bore. In reduced bore valves, the valve opening is smaller than the diameter of the piping; in full bore valves, the valve opening is the same size as the diameter of the piping. Full bore ball valves are often valued because they minimize the pressure drop across the valve.
Balls valves are usually only recommended for use in the fully open or fully closed position. They are not suited to regulate flow by being kept partially open because ball valves make use of a ring-shaped soft valve seat.
When used in the partially open position, pressure is applied to only a portion of the valve seat, which can cause it to deform. If the valve seat deforms, its sealing properties are impaired and it will leak as a result.
Butterfly Valves
In butterfly valves, the flow is regulated through a disc-type element held in place in the center of the valve by a rod. Similar to ball valves, valve operation time is short because the valving element is simply rotated a quarter turn (90°) to open or close the passageway.
Steam Valve Sizing Calculator
Butterfly valves are characterized by their simple construction, lightness in weight, and compact design. Their face-to-face dimension is often extremely small, making the pressure drop across a butterfly valve much smaller than globe valves (see below). Materials used for the valving element and sealing can limit their applications at higher temperatures or with certain types of fluids. Butterfly valves are often used on applications for water and air, and in applications with large pipe diameters.
Globe Valves
The globe valve is suitable for use on a wide variety of applications, from flow rate control to open/close operation.

In this type of valve, flow rate control is determined not by the size of the opening in the valve seat, but rather by the lift of the valve plug (the distance the valve plug is from the valve seat). One feature of globe valves is that even if used in the partially open position, there is less risk of damage to the valve seat or valve plug by the fluid than with other types of manual valves. Among the various configurations available, needle type globe valves are particularly well suited for flow rate control.
Another point to consider about globe valves is that the pressure drop across the valve is greater than that of many other types of valves because the passageway is S-shaped. Valve operation time is also longer because the valve stem must be turned several times in order to open and close the valve, and this may eventually cause leakage of the gland seal (packing). Furthermore, care must be taken not to turn the valve shaft too far because there is a possibility it could damage the seating surface.
Gate Valves
The construction of a gate valve is similar to that of a floodgate: flow is controlled by raising or lowering the valving element, which is generally available in three different types: solid (plain), flexible, and split. The latter two types help prevent the valving element and body from being deformed due to various operating conditions.
Like ball valves, gate valves are not usually used to regulate flow. One of the reasons for this is because the valving element can be damaged when in the partially open position. Similarly, they also limit the pressure drop across the valve when fully open. However, setting the valve to the fully open or closed position requires the handle to be turned many times, which generally makes these valves have the longest operating times among those valve types mentioned here.
Diaphragm Valves
Diaphragm valves use a 'pinching' method to stop the valve flow using a flexible diaphragm. They are available in two types: weir and straight-way. The most commonly seen of the two is the weir-type. This is because the straight-way type requires additional stretching of the diaphragm, which can shorten the diaphragm's life-span.

One of the major advantages of using diaphragm valves is that the valve components can be isolated from the process fluid. Similarly, this construction helps prevent leakage of the fluid without the use of a gland seal (packing) as seen in other types of valves. One the other hand, the diaphragm becomes worn more easily and regular maintenance is necessary if the valve is used on a regular basis. These types of valves are generally not suited for very high temperature fluids and are mainly used on liquid systems.
Note: There exists a valve for steam systems that goes by a similar name. It is an automated valve with a diaphragm type actuator. This is often shortened to just 'diaphragm valve', so when a valve is referred to by this name, care must be taken to verify which type of valve it is.
Improving Compressed Air Quality and Countermeasures Against Leaks | Check Valve Installation and Benefits |
Also on TLV.com

This article is not focused to any specific aspect of steam control valve. The wide subject matter can accommodate a lot of pages. However, to confine it within a respectable size, we will focus mostly on technicalities and industrial applications of steam control valve. We will try to make this article interesting for all readers, and navigate from basics to complex technology-oriented topics.
Let’s hit at the root of the subject, which is steam in this article.
What is Steam and what are its principal applications?
Water is converted to steam during transition from liquid to gas. Hydrogen bonds keep the H2O molecules together, and it breaks free to generate steam. In the liquid form, the molecules are continuously broken and joined with each other. The bond of the molecules becomes loose with application of heat, and eventually some molecules will break free at higher heat and create steam or dry steam. Both dry and wet steam is used in industries. Wet steam is formed when some water molecules release its’ latent heat and form tiny water droplets.
Steam is used in a large number of industrial applications. The most common applications are the process heating and driving the steam turbines to generate electricity. Apart from these, steam is used for atomization, cleaning, moisturize, and humidification. However, most of the applications will require some parameter control, and thus a steam control valve becomes a part of process control engineering.
Why a Steam Control Valve is used in process control applications?
Technically, a valve is a device which will control flow of fluid or vapor in any system. In case of steam, the major applications are to reduce the pressure of the inlet steam for process application. However, in addition to controlling pressure, a steam control valve will also control temperature.
Boilers will typically work at high pressures, as low pressure operation will result in carryover of water. High pressure steam has lower specific volume, which will allow pipes to carry less weight. In effect, distribution of steam becomes easier and cheaper due to the cost reduction in piping and insulation. Industrial process applications use steam at a lower pressure. The reason for this is that the steam at a low pressure has higher latent heat, which increases energy efficiency to a large extent. Steam pressure and temperature are related, and hence temperature is automatically controlled through the control of steam pressure. The reduction of steam pressure is also related to the required plant safety. Steam pressure can be controlled by using Steam Control Valve.
What is the principle of operation of a Steam Control Valve?
The old method of throttling flow or using an orifice plate will result in fluctuations of flow rate. The ideal solution is to adjust the downstream pressure automatically through proportional adjustment of valve opening. This technique will keep the steam pressure unaltered even during the fluctuations of flow rate.
Fig-1
The schematic in Fig-1 illustrates the use of a Steam Control Valve to reduce steam pressure to control heating inside the jacketed vessel. This system will ideally demand for manual interventions. A fully self-contained automatic system will comprise of an actuated Steam Control Valve, a pressure sensor and an actuator. This kind of system senses the fluctuations in the downstream pressure and adjusts it through a quick response actuator.
The typical mechanism to adjust the outlet pressure is through a balance of force adjustment between the steam pressure and the adjustment spring in the valve. The steam control valve is manufactured either by Non-piloted Acting Valve or Pilot-operated Acting Valve.

The non-piloted adjustment spring applies downward force directly on the main valve. The Piloted type adjustment spring executes downward pressure on a smaller pilot valve, which is not the same as the main valve.
The advantages of direct acting type are compact, economic, and straightforward installation. However, the controlling factor have larger variations from the set point, and mostly used for low loads.
Fig-2
The schematic in Fig-2 above is self-explanatory of the Piloted type Steam Control Valve arrangement normally used for a Heat Load along with a Heat Exchanger. The piloted type is used for heavy loads to achieve a fast response in a much broader range of flow range than the non-piloted types. However, these are larger in size and costlier.
What are the industrial applications of Steam Control Valves?
Steam is the mostly used medium for heat transfer in process control applications in industries. Steam Control Vales are largely used in steam driven turbines in electric power plants. The range of applications is quite large. However, Food-processing plants, Refineries and chemical plants are the users of different types of control valves driven by steam.
Here is a list of some typical applications of this valve:
- Fluid heat exchangers
- Re-boilers
- Reactors
- Combustion air pre-heaters
- Sterilizers
- Unit Heaters
- Humidifiers
- Direct Steam Injection Sanitary Heater
- Ironers
- Acid baths
- Small storage calorifiers
- Water treatment plants
Conclusion:
We may conclude that steam control valve is a significant equipment to manufacture high-quality products in industries. Today, advanced technology and long lasting materials are used to manufacture these valves to prolong its life cycle. It is also imperative that process control engineers have to learn installation and application techniques of this important industrial equipment.
OMC V100: DIN rated, PN flanged control valves. Typically used for Steam, Water and Gas applications. Can be provided with Class V or Class VI shutoff. Provide compact solution with pneumatic or electric actuators and positioners. |
OMC K100: A larger range of body materials and trim capability. This range of valves is particularly suited to applications where aggresive fluids and demanding applications require control valves with exotic materials or reduced trim. |
OMC KA10: True ANSI specification valves. This means that face to face dimensions as well as flanges conform to the requirements of ANSI standards. |
OMC S100: Control valve for food processing, chemical and cosmetic industries, these valves are manufactured with hygenic internals and a range of triclamp or sanitry process connections. |
We have limited stock of small bore (1/2' and 1') bossmatic control valves. These are available with I/P positions and a full set of service spares |
OMC K150: 3-Port Mixing / Diverting Control Valve for flow suitable for DHW (Hot water systems, including temperature control of plate heat exchangers and calorifiers. |
OMC S250 is used in the industrial sectors such as the food, pharmaceutical, chemical and cosmetic industries, where high hygienic standards are required.these valves are manufactured with hygenic internals and a range of triclamp or sanitry process connections. |
OMC S260 is used in the food, pharmaceutical, chemical and cosmetic industries, where high hygienic standards are required. These valves are manufactured with hygenic internals and a range of triclamp or sanitry process connections. |
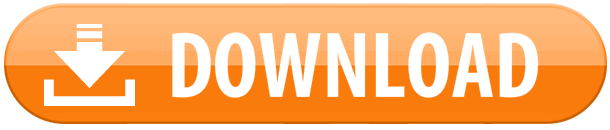